What is Porosity in Welding: Typical Resources and Efficient Solutions
What is Porosity in Welding: Typical Resources and Efficient Solutions
Blog Article
Porosity in Welding: Identifying Common Issues and Implementing Best Practices for Prevention
Porosity in welding is a prevalent issue that commonly goes undetected till it creates significant problems with the stability of welds. This usual defect can endanger the strength and resilience of bonded structures, posturing safety threats and resulting in pricey rework. By recognizing the source of porosity and carrying out efficient prevention strategies, welders can substantially boost the top quality and dependability of their welds. In this discussion, we will certainly explore the essential variables adding to porosity formation, analyze its detrimental impacts on weld performance, and go over the most effective techniques that can be taken on to decrease porosity incident in welding processes.
Common Root Causes Of Porosity
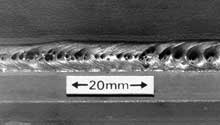
Another constant offender behind porosity is the visibility of contaminants on the surface of the base steel, such as oil, oil, or corrosion. When these contaminants are not successfully gotten rid of before welding, they can vaporize and become entraped in the weld, causing defects. In addition, using filthy or damp filler products can present contaminations right into the weld, adding to porosity problems. To alleviate these common causes of porosity, thorough cleansing of base steels, correct shielding gas selection, and adherence to optimal welding criteria are important practices in attaining high-quality, porosity-free welds.
Impact of Porosity on Weld High Quality

The presence of porosity in welding can substantially endanger the structural integrity and mechanical homes of bonded joints. Porosity develops spaces within the weld metal, compromising its total toughness and load-bearing ability. These spaces act as stress and anxiety focus points, making the weld extra susceptible to splitting and failing under used tons. Furthermore, porosity can lower the weld's resistance to rust and other environmental elements, additionally decreasing its long life and performance.
Welds with high porosity levels tend to exhibit reduced impact strength and lowered capacity to deform plastically before fracturing. Porosity can hamper the weld's ability to efficiently transmit pressures, leading to early weld failing and prospective security hazards in crucial frameworks.
Ideal Practices for Porosity Avoidance
To boost the architectural stability and high quality of welded joints, what specific measures can be applied to he has a good point decrease the incident of porosity during the welding procedure? Making use of the proper welding method for the particular product being welded, such as changing the welding angle and weapon setting, can further avoid porosity. Regular assessment of welds and prompt removal of any type of issues determined during the welding procedure are necessary practices to protect against porosity and create premium welds.
Importance of Appropriate Welding Strategies
Executing appropriate welding techniques is vital in guaranteeing the architectural stability and top quality of bonded joints, developing upon the structure of efficient porosity avoidance procedures. Welding techniques straight impact the overall toughness and toughness of the bonded framework. One vital element of appropriate welding strategies is keeping the appropriate heat input. Excessive warmth can bring about boosted porosity because of the entrapment of gases in the weld swimming pool. On the other hand, inadequate warm might result in incomplete blend, developing prospective powerlessness in the joint. In addition, using the proper welding criteria, such as voltage, present, and take a trip speed, is crucial for accomplishing audio welds with very little porosity.
Moreover, the selection of welding process, additional hints whether it be MIG, TIG, or stick welding, ought to line up with the details requirements of the project to ensure optimal results. Correct cleaning and prep work of the base metal, as well as picking the ideal filler product, are additionally essential components of skilled welding strategies. By adhering to these finest techniques, welders can minimize the danger of porosity formation and generate high-quality, structurally sound welds.

Testing and Quality Assurance Procedures
Quality assurance measures play a critical role in verifying the honesty and dependability of weblink welded joints. Testing treatments are important to detect and avoid porosity in welding, making sure the toughness and longevity of the end product. Non-destructive screening approaches such as ultrasonic screening, radiographic screening, and aesthetic assessment are commonly utilized to determine potential issues like porosity. These techniques permit the evaluation of weld high quality without jeopardizing the integrity of the joint. What is Porosity.
Conducting pre-weld and post-weld assessments is also essential in maintaining high quality control criteria. Pre-weld evaluations involve confirming the products, tools settings, and tidiness of the workspace to avoid contamination. Post-weld examinations, on the other hand, examine the final weld for any kind of flaws, consisting of porosity, and verify that it meets specified standards. Applying a comprehensive quality control plan that includes thorough testing procedures and evaluations is vital to minimizing porosity issues and making sure the total top quality of welded joints.
Conclusion
Finally, porosity in welding can be an usual issue that affects the high quality of welds. By recognizing the common root causes of porosity and applying ideal practices for prevention, such as appropriate welding methods and screening actions, welders can ensure top quality and reputable welds. It is necessary to focus on prevention methods to reduce the incident of porosity and preserve the stability of bonded structures.
Report this page